CSJ Company: A Leader in Silicone Sealant Manufacturer
Established in 1993, CSJ Company is a renowned high-tech enterprise based in Foshan, Guangdong, China. We specialize in the research, production, and sales of innovative sealant solutions.
As a leading manufacturer and supplier, we offer a wide range of high-quality chemical products for diverse industries, including construction, automotive, machinery, electronics, and solar photovoltaic. Our state-of-the-art facilities, including bottle injection molding, color printing, and automated assembly lines, ensure efficient and precise production processes.
To guarantee product quality and stability, we have formed long-term strategic partnerships with industry giants like Wacker and Dow Corning. Our pursuit to excellence has positioned CSJ Company as a prominent and influential player in China’s silicone rubber industry.
About UsCSJ Hot-Sale Products
Why Choose CSJ as Silicone Sealant Supplier
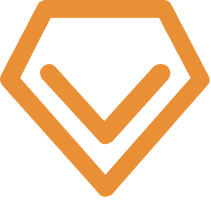
1. A Proven Track Record : With over 30 years of experience in the silicone adhesive industry, we have a deep understanding of market trends and customer needs. Our pursuit to quality and innovation has allowed us to develop a range of reliable and high-performance silicone adhesive products.
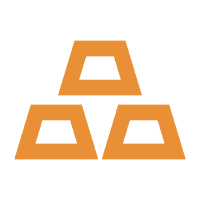
2. Premium Raw Materials : We source our raw materials from renowned German chemical suppliers, known for their stringent quality standards. These high-quality materials ensure that our silicone adhesives exhibit exceptional performance in terms of bonding strength, weather resistance, and water resistance.
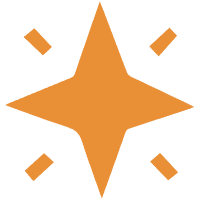
3. Integrated Production for Quality Assurance : To maintain the highest quality standards, we have integrated our packaging bottle production process. By controlling the entire production chain, from raw material selection to final packaging, we ensure that our silicone adhesives reach you in optimal condition.
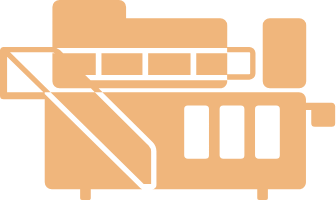
4. Advanced Technology, Efficient Production :Our state-of-the-art production lines enable us to produce high-quality silicone adhesives efficiently. Automated processes and rigorous quality control measures guarantee consistent product performance and reliability.
Common Applications of Silicone Sealant
Silicone sealant is a versatile product with numerous applications, both indoors and outdoors. Here are some of the most common uses:
Bathroom
Sealing gaps around bathtubs, showers, sinks, and tiles to prevent water damage and mold growth.
Kitchen
Sealing gaps around sinks, countertops, and appliances to prevent water damage and pest infestations.
Windows and Doors
Sealing gaps around windows and doors to improve energy efficiency and reduce drafts.
Automotive
Sealing gaps around windows, doors, and other components.
Industrial Applications
Sealing joints and seams in machinery and equipment.
Aquariums
Sealing joints in aquariums to prevent leaks.
Curtain Wall
Sealing the joints between curtain wall panels to create a continuous and weatherproof barrier.
Decoration Caulking
Sealing gaps between baseboards and walls to prevent moisture damage.
Silicone Sealant Manufacturing Process
Silicone sealant is a versatile product with numerous applications, from construction to automotive. Here’s a simplified overview of the manufacturing process:
1. Raw Material Preparation:
- Silicone Base: This is the primary component, a polymer derived from silicon.
- Cross-Linking Agent: This substance triggers the curing process, transforming the liquid sealant into a solid rubber-like material.
- Filler: These are added to improve the sealant’s properties, such as adhesion, flexibility, and durability. Common fillers include silica, titanium dioxide, and calcium carbonate.
- Catalysts: These accelerate the curing process.
- Plasticizers: These enhance the sealant’s flexibility and workability.
2. Mixing:
- All the raw materials are carefully measured and mixed in a controlled environment.
- The mixing process ensures a homogeneous blend, which is crucial for the final product’s performance.
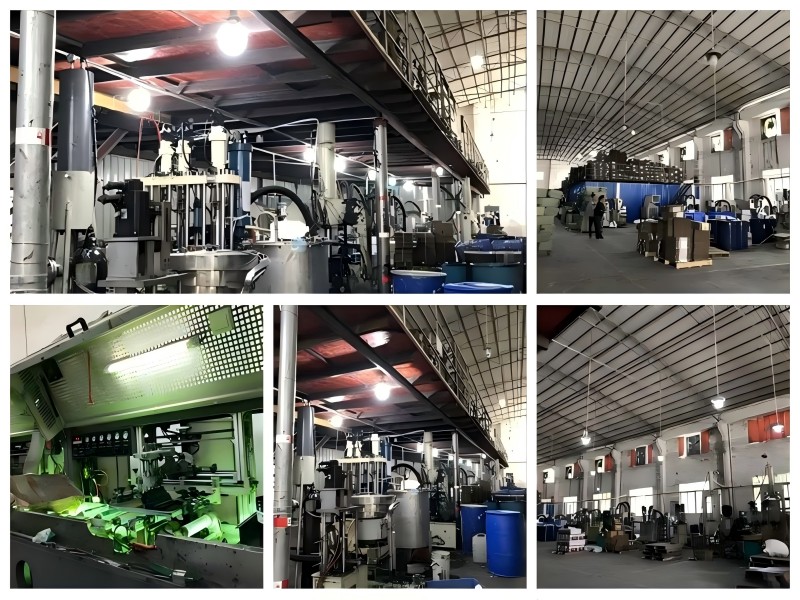
3. Deaeration:
- The mixed sealant is subjected to a vacuum process to remove air bubbles. This step is essential for preventing defects and ensuring a smooth, bubble-free application.
4. Packaging:
- The deaerated sealant is dispensed into cartridges or sausages, ready for use.
5. Quality Control:
- Throughout the manufacturing process, rigorous quality control measures are implemented to ensure that the final product meets specific standards.
- This includes testing for viscosity, adhesion, curing time, and other relevant properties.
What Our Other Customers Say About Us
After-Sales Support
1. Expert Technical Support
We offer comprehensive technical support, including expert advice on product selection, application techniques, and troubleshooting. Our skilled team is ready to assist you with your specific project needs.
2. Quality Assurance and After-Sales Service
We prioritize quality and customer satisfaction. Our products are backed by a warranty, and we offer prompt after-sales support to address any issues. We actively gather customer feedback to continuously improve our products and services.
3. Comprehensive Training
We provide training programs to help you maximize the benefits of our silicone sealants. Our training sessions cover product knowledge, application techniques, and industry best practices.
4. Reliable Logistics and Distribution
We partner with trusted logistics providers to ensure timely and efficient delivery of your orders. We offer flexible shipping options to meet your specific needs.
5. Dedicated Customer Support
We value your feedback and are committed to resolving any issues promptly. Our dedicated customer support team is ready to assist you with any questions or concerns.
Silicone Sealant FAQs
Silicone sealant typically takes 24-48 hours to cure to the touch and 72 hours for full cure. However, curing time can vary depending on factors like temperature, humidity, and the specific product.
While some silicone sealants can be painted over, it’s important to choose a paint specifically designed for use with silicone. Always consult the product’s label for specific instructions.
To remove old silicone sealant, you can use a utility knife or a specialized sealant removal tool. Apply a silicone sealant remover to soften the sealant, then scrape it off with a putty knife.
Yes, silicone sealant can be used on porous surfaces like concrete and brick. However, it’s essential to ensure the surface is clean, dry, and free of any contaminants before applying the sealant.
Silicone sealant typically works best in temperatures between 50°F and 90°F (10°C to 32°C). Avoid applying it in extreme cold or hot temperatures.
The lifespan of silicone sealant vary depending on the specific product. And the quality of high-quality silicone sealants can last for many years when properly applied and maintained.