مقدمة
يُعد مانع التسرب السيليكوني مغيّرًا لقواعد اللعبة في تطبيقات الإنشاءات الحديثة والسيارات والتطبيقات الصناعية. على عكس المواد المانعة للتسرب التقليدية، توفر التركيبات القائمة على السيليكون متانة ومرونة ومقاومة استثنائية لدرجات الحرارة القصوى والعوامل البيئية. بدءًا من إحكام إغلاق النوافذ في المباني الشاهقة إلى ضمان عدم تسرب المواد المانعة للتسرب في السيارات، أصبحت مواد السيليكون المانعة للتسرب جزءًا لا غنى عنه في حياتنا اليومية.
ولكن هل تساءلت يومًا كيف مانع تسرب السيليكون مصنعة؟ ما الذي يجعلها مرنة ومتعددة الاستخدامات؟ يتعمق هذا الدليل في عملية تصنيع مانع تسرب السيليكون، ويسلط الضوء على المواد الخام وتقنيات التصنيع وإجراءات مراقبة الجودة وجهود الاستدامة. سواءً كنت مقاولاً أو متحمسًا لصنعه بنفسك أو محترفًا في هذا المجال، فإن فهم العلم وراء مانع تسرب السيليكون سيساعدك على اتخاذ قرارات مستنيرة عند اختيار المنتج المناسب لاحتياجاتك.
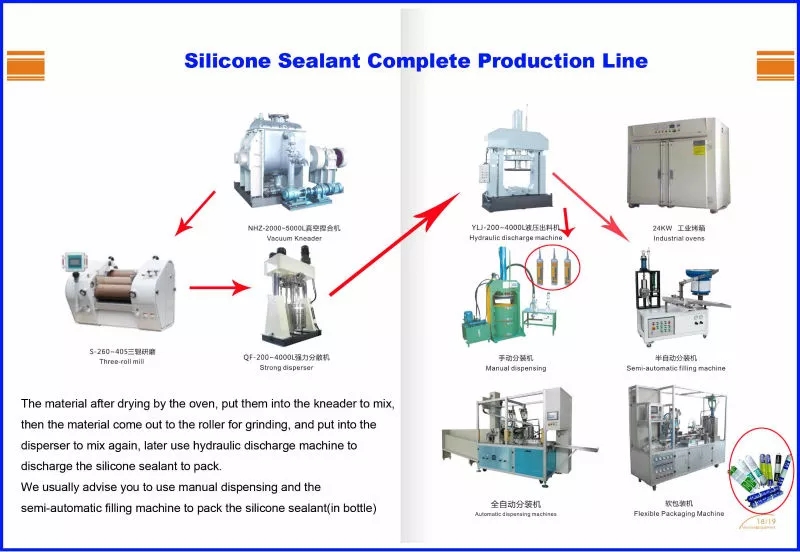
ما هو مانع تسرب السيليكون؟
مانع التسرب السيليكوني عبارة عن مادة لاصقة مرنة تشبه المطاط مصممة لتوفير إحكام الإغلاق والترابط والعزل طويل الأمد. وعلى عكس المواد المانعة للتسرب المصنوعة من الأكريليك أو البولي يوريثين، تظل التركيبات القائمة على السيليكون مرنة حتى بعد المعالجة، مما يجعلها فعالة للغاية في البيئات التي تتسم بتقلبات درجات الحرارة والرطوبة والتعرض للمواد الكيميائية.
الخواص الفريدة لمانع تسرب السيليكون
- الاستقرار الحراري: يمكن أن تتحمل الحرارة والبرودة الشديدة، مما يجعلها مثالية للاستخدامات الداخلية والخارجية.
- مقاومة الماء: يشكل مانع تسرب المياه، مما يمنع التسربات والأضرار الناجمة عن الرطوبة.
- المرونة والمرونة: يحافظ على شكله والتصاقه حتى في المفاصل عالية الحركة.
- مقاومة المواد الكيميائية والأشعة فوق البنفسجية: لا تتحلل عند تعرضها للظروف الجوية القاسية أو المواد الكيميائية أو الأشعة فوق البنفسجية.
- طول العمر: يمكن لمانعات التسرب السيليكونية أن تدوم من 10 إلى 20 عاماً، متفوقةً بذلك على العديد من أنواع مانعات التسرب الأخرى.
كل يوم التطبيقات مانع تسرب السيليكون
- البناء وتحسين المنزل: يستخدم لإحكام إغلاق النوافذ والأبواب وأحواض الاستحمام وأحواض المطبخ لمنع تسرب المياه وتيارات الهواء.
- السيارات والفضاء الجوي: ضرورية في حشيات المحركات، والزجاج الأمامي، ومكونات الطائرات من أجل المتانة في الظروف القاسية.
- الإلكترونيات والأنظمة الكهربائية: تحمي لوحات الدارات الكهربائية والأسلاك من الرطوبة والغبار وتقلبات درجات الحرارة.
- الاستخدامات الطبية والغذائية: يوجد في الأجهزة الطبية وأدوات المطبخ نظراً لخصائصه غير السامة والمقاومة للحرارة.
المواد الخام المستخدمة في تصنيع مانع تسرب السيليكون
تكمن فعالية مانع تسرب السيليكون في المواد الخام المختارة بعناية. يلعب كل مكون دورًا حاسمًا في تحديد أداء المادة المانعة للتسرب وقوامها وطول عمرها.
1. بوليمرات السيليكون
توفر بوليمرات السيليكون (السيلوكسانات) العمود الفقري لمواد السيليكون المانعة للتسرب المرونة ومقاومة الماء والاستقرار الحراري. يتم تصنيع هذه البوليمرات من خلال عمليات كيميائية تتضمن السيليكون والأكسجين والمركبات العضوية.
2. الحشوات والتعزيزات
تعمل مواد الحشو مثل السيليكا المدخنة وكربونات الكالسيوم والطين على تعزيز الخواص الميكانيكية والتحكم في اللزوجة وتحسين تكاليف الإنتاج. تعمل التعزيزات على تحسين قوة ومتانة المادة المانعة للتسرب، مما يضمن التصاقها جيدًا بالأسطح المختلفة.
3. المحفزات وعوامل المعالجة
تؤثر عوامل المعالجة المختلفة، بما في ذلك حمض الأسيتيك والأوكسيم والأنظمة القائمة على الألكوكسي، على كيفية تصلب مانع التسرب السيليكوني. تتفاعل التركيبات المعالجة بالرطوبة مع الرطوبة في الهواء، بينما تتطلب التركيبات المعالجة بالحرارة درجات حرارة مرتفعة لتثبت بشكل صحيح.
4. المواد المضافة والمثبتات
ولزيادة تحسين الالتصاق واللون ومقاومة العوامل البيئية، تدمج الشركات المصنعة مثبتات الأشعة فوق البنفسجية ومحفزات الالتصاق ومبيدات الفطريات لمنع نمو العفن في البيئات الرطبة.
مانع التسرب السيليكوني عملية التصنيع
يتضمن إنتاج مانع التسرب السيليكوني عدة خطوات معقدة لتحقيق التوازن الصحيح بين اللزوجة والالتصاق وخصائص المعالجة.
1. الخلط والمزج
يتم خلط المواد الخام، بما في ذلك بوليمرات السيليكون والمواد المالئة والمواد المضافة، في معدات صناعية متخصصة لإنشاء قوام موحد يشبه العجينة.
2. نزع الهواء والتجانس
يمكن لفقاعات الهواء المحتبسة في الخليط أن تضعف المنتج النهائي. وللقضاء على هذه المشكلة، يخضع المزيج إلى نزع الهواء بالتفريغلضمان الحصول على مادة مانعة للتسرب ناعمة وخالية من الفقاعات.
3. إضافة عوامل المعالجة والعوامل الحفازة
في هذه المرحلة، يتم دمج عوامل المعالجة في التركيبة. ويعتمد اختيار نظام المعالجة (الأسيتوكسي أو المحايد أو الأوكسيمي) على الاستخدام المقصود لمانع التسرب.
4. اختبار الجودة وتقييم الاستقرار
قبل التغليف، يخضع مانع التسرب السيليكوني لاختبارات صارمة لمراقبة الجودة، بما في ذلك:
- اللزوجة ومعدل التدفق: ضمان الاتساق المناسب للتطبيق السلس.
- قوة الالتصاق: قياس قدرات الترابط على الأسطح المختلفة.
- مقاومة للحرارة والطقس: تقييم الأداء تحت درجات الحرارة القصوى والتعرض للأشعة فوق البنفسجية.
5. التعبئة والتغليف والتوزيع
يتم تعبئة المنتج النهائي في خراطيش أو أنابيب أو حاويات سائبة، جاهزة للاستخدام الاستهلاكي والصناعي. يتضمن الوسم المناسب تعليمات الاستخدام واحتياطات السلامة وتواريخ انتهاء الصلاحية.
مراقبة الجودة في تصنيع مانع تسرب السيليكون
للحفاظ على معايير المنتج الفائقة، تطبق الشركات المصنعة إجراءات صارمة لضمان الجودة في كل مرحلة من مراحل التصنيع.
إجراءات الاختبار الرئيسية
- وقت المعالجة واختبارات المرونة: التأكد من تثبيت المادة المانعة للتسرب بشكل صحيح والاحتفاظ بمرونتها.
- مقاومة المواد الكيميائية والمذيبات: التحقق من المتانة عند التعرض للمنظفات المنزلية والوقود والمواد الكيميائية الصناعية.
- اختبار الإجهاد البيئي: محاكاة سنوات من التعرض للطقس في ظروف معملية متسارعة.
الأثر البيئي والاستدامة
مع تحول الصناعات نحو الحلول الصديقة للبيئة، تستكشف الشركات المصنعة لمواد السيليكون المانعة للتسرب السيليكونية طرقًا لتقليل بصمتها الكربونية.
1. تطوير مواد مانعة للتسرب من السيليكون منخفضة المركبات العضوية المتطايرة ومواد السيليكون الخضراء
تقدم العديد من الشركات الآن مواد مانعة للتسرب منخفضة المركبات العضوية المتطايرة (مركبات عضوية متطايرة) تقلل من تلوث الهواء والمخاطر الصحية. بالإضافة إلى ذلك، بدأت مواد مانعات التسرب المصنوعة من السيليكون ذات الأساس المائي في الظهور كبديل مستدام.
2. مبادرات إعادة التدوير والحد من النفايات
يتبنى المصنعون أنظمة إعادة التدوير ذات الحلقة المغلقة، وإعادة استخدام نفايات الإنتاج، واستخدام العبوات القابلة للتحلل الحيوي للحد من الأثر البيئي.
الأسئلة الشائعة
1. ما هو العمر الافتراضي لمانع تسرب السيليكون؟
تدوم معظم مانعات تسرب السيليكون من 12-24 شهرًا عند تخزينها في بيئة باردة وجافة. ويؤدي إحكام إغلاق الأنابيب المفتوحة بشكل صحيح إلى إطالة فترة الاستخدام.
2. هل يمكن استخدام مانع تسرب السيليكون في الهواء الطلق؟
نعم, مانعات تسرب السيليكون المقاومة للعوامل الجوية مصممة للاستخدام الخارجي، وتوفر مقاومة فائقة للأشعة فوق البنفسجية والماء ودرجات الحرارة.
3. كيف يمكنني إزالة مانع تسرب السيليكون من الأسطح؟
بالنسبة للسيليكون غير المعالج، استخدم الكحول المحمر أو الأسيتون. أما بالنسبة للسيليكون المعالج، فإن الإزالة الميكانيكية باستخدام مكشطة أو مزيل سيليكون متخصص تكون فعالة.
4. هل مانع تسرب السيليكون آمن للتلامس مع الطعام؟
مواد مانعة للتسرب مصنوعة من السيليكون المخصص للطعام بدون مواد كيميائية ضارة، مما يجعلها مناسبة لبيئات المطبخ ومعالجة الطعام.
5. ما المدة التي تستغرقها مادة السيليكون المانعة للتسرب حتى تعالج؟
يختلف وقت المعالجة باختلاف الرطوبة ودرجة الحرارة والسماكة. تعالج معظم مانعات التسرب السيليكونية بالكامل في غضون 24-48 ساعة، ولكن بعض الأنواع سريعة المعالجة تثبت في غضون ساعات قليلة.
الخاتمة
يُعد مانع التسرب السيليكوني أكثر من مجرد مادة لاصقة - فهو مكون أساسي في البناء والسيارات والإلكترونيات وغيرها. يتيح فهم عملية تصنيعها وخصائصها وتطبيقاتها للمستخدمين اتخاذ خيارات مستنيرة لتلبية احتياجاتهم من المواد المانعة للتسرب.
مع استمرار الصناعة في الابتكار بتركيبات مستدامة وعالية الأداء، ستظل مواد السيليكون المانعة للتسرب المصنوعة من السيليكون خياراً مفضلاً للمحترفين وأصحاب المنازل على حد سواء. سواءً كان ذلك لإغلاق حوض الحمام أو تجميع طائرة أو حماية الدوائر الإلكترونية، فإن اختيار مانع التسرب السيليكوني المناسب يضمن نتائج موثوقة تدوم طويلاً.