Alcohol-type vs. oxime-type silicone adhesive: The ultimate guide to adhesive selection with 10,000 words
Abstrakt:
In the field of construction and industrial bonding, the choice of silicone glass adhesive is far from as simple as “neutral” or “acidic”. The “alcohol-type” and “oxime-type” classifications hidden under the packaging label are actually the key code to determine the success or failure of sealing. This article deeply analyzes the core differences between the two in chemical nature, physical properties, application scenarios and construction processes: from the chemical mechanism of cross-linking agents to the performance of bonding strength, from bubble pain point analysis to climate adaptation strategies, combined with authoritative research and industry standards, to build a complete decision-making framework for scientific adhesive selection for you, helping you to accurately lock in the optimal solution in complex working conditions.
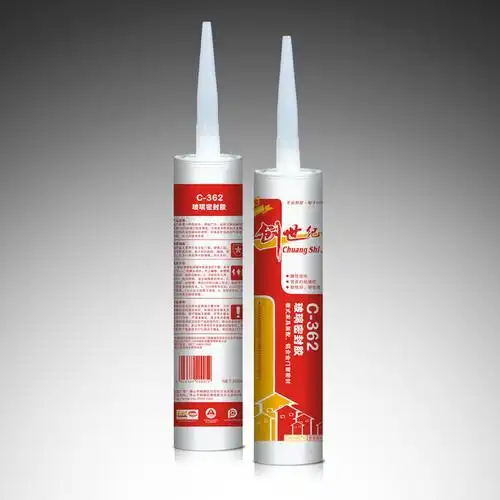
1. Basics of silicone adhesive: single-component and double-component and acid-base division
Modern silicone adhesive dominates the market in the form of single component. It solidifies by absorbing moisture in the air, and its construction convenience far exceeds that of double-component products that need to be mixed and solidified. According to chemical properties, silicone adhesive is divided into acidic adhesive and neutral adhesive: although acidic adhesive is cheap and has strong adhesion to glass, it is easy to corrode metals due to the release of acetic acid and has limited reaction with alkaline substrates; neutral adhesive uses alcohol or oxime crosslinkers to avoid corrosion and has a wider range of applications, becoming the mainstream choice for current building sealing.
2. Chemical nature of alcohol and oxime types: silent revolution of crosslinkers
The fundamental difference between alcohol and oxime types comes from the chemical structure of their crosslinkers:
- Alcohol adhesive: releases small alcohol molecules (such as methanol) during curing, and the reaction is mild;
- Oxime adhesive: releases oxime compounds (such as acetone oxime) during curing, and has higher activity.
This directly leads to the performance division between the two. Studies have shown that the molecular structure of the crosslinking agent directly affects the density of the colloid crosslinking network (see Related research from the American Chemical Society), which in turn determines the final mechanical performance.
3. Physical performance showdown: strength, temperature resistance and durability
- Bond strength: Oxime-type adhesives can form a denser network with highly active crosslinkers, and show excellent bonding to difficult-to-bond substrates such as metals and plastics (about 20-30% higher than alcohol-type adhesives), especially suitable for key areas such as curtain wall structure bonding.
- Heat resistance level: The temperature resistance range of alcohol-type adhesives is usually -40℃ to 120℃, while high-quality oxime-type adhesives can withstand extreme tests of -60℃ to 150℃, providing protection for the sealing of industrial equipment (in compliance with ISO 11600 standard requirements).
- Shelf life: The stability of the cross-linking agent determines the life of the product. The general shelf life of alcohol-type adhesive is 6-9 months, while that of oxime-type adhesive can reach 9-12 months, with significant storage advantages.
4. Differentiation of application scenarios: the game between general and professional
- Broad advantage of alcohol-type adhesive: Because it is non-corrosive and has good compatibility with most substrates, it has become a “universal choice” for caulking doors and windows and bonding ordinary building materials. However, it should be noted that its structural strength is limited, and it is sensitive to the humidity of the substrate surface, and the bonding force drops sharply in a humid environment.
- Deep specialization of oxime-type adhesive: It is irreplaceable in the industrial field (such as metal frame bonding, electronic component packaging). However, it has a corrosion risk to copper materials, and the technical threshold is high-inferior oxime-type adhesive is prone to shrinkage and cracking at low temperatures, and it is crucial to choose a well-known brand (such as referring to the [Recommended List of China Architectural Glass and Industrial Glass Association] (http://www.glass.org.cn/)).
5. Construction pain point solution: the truth about bubbles and cracks
Common bubble problems in summer construction are mostly caused by methanol released when alcohol-type glue is cured. Methanol evaporates violently at high temperature (>50℃). If it is blocked by a dense substrate (such as concrete, metal), the gas will break through the uncured colloid to form bubbles. However, there is almost no gas release during the curing of oxime-type glue, which eliminates the hidden danger of bubbles from the source. However, when oxime-type glue is used in cold winter construction, if the formulation process is insufficient (such as improper selection of plasticizer), the colloid shrinkage stress is too large to cause cracks, highlighting the importance of high-quality products.
6. Economic efficiency and environmental adaptation: the art of balancing cost and efficiency
Due to the high cost of raw materials and technology, the price of oxime-type glue is usually 20%-30% higher than that of alcohol-type glue. Users need to be wary of abnormally low-priced products: if the quality of oxime-type cross-linking agents does not meet the standards, performance and durability will be seriously sacrificed. China has a vast territory, and the selection of glue needs to be adapted to local conditions:
- Southern high temperature and high humidity area: Prioritize oxime glue with excellent anti-bubble performance;
- Northern severe cold and dry zone: Low temperature resistant formula alcohol glue or strictly verified anti-cracking oxime glue needs to be selected.
7. Industry Trend: Double Helix Evolution of Environmental Protection and High Performance
As environmental regulations become stricter (such as the EU REACH Regulation restricting harmful solvents), new alcohol glues with low VOC and no methanol release are being developed. At the same time, modified oxime glues continue to make breakthroughs in improving low temperature resistance and reducing shrinkage, such as the use of silane-modified polyether technology (Related Patent Progress), blurring the traditional performance boundaries.
Summary:
Alcohol-type and oxime-type silicone adhesives are not simply a contest of superiority and inferiority, but two technical paths to solve different engineering challenges. Alcohol-type adhesives, with their wide applicability and economy, protect the sealing needs of daily buildings; oxime-type adhesives, with their excellent bonding strength and stability, support the demanding mission in the industrial field. A wise choice requires us to penetrate the surface label of “neutral adhesive” and gain insight into the three-dimensional matrix of substrate characteristics, environmental factors and mechanical requirements – between the flexibility of alcohol-type and the toughness of oxime-type, find the bonding wisdom that best suits the current challenges. With the continuous evolution of technology, silicone adhesives in the future will achieve the unity of environmental protection and performance in a higher dimension, providing a more reliable “invisible skeleton” for building the world.