Decoding Glass Glue: The Invisible Guardian from Home Improvement to Skyscrapers
Περίληψη:
Glass glue is far from a simple “adhesive”. It is an indispensable crystallization of chemical wisdom in modern construction and manufacturing, playing a key role in sealing and leakproofing, structural reinforcement, and beautiful decoration. This article will deeply analyze the core common sense of glass glue, covering its curing principle, the precise application of acidic/neutral glue, the excellent performance of structural sealants, scientific construction points, color aesthetics and future innovation trends, revealing how this “invisible hero” silently guards our building safety and quality of life.
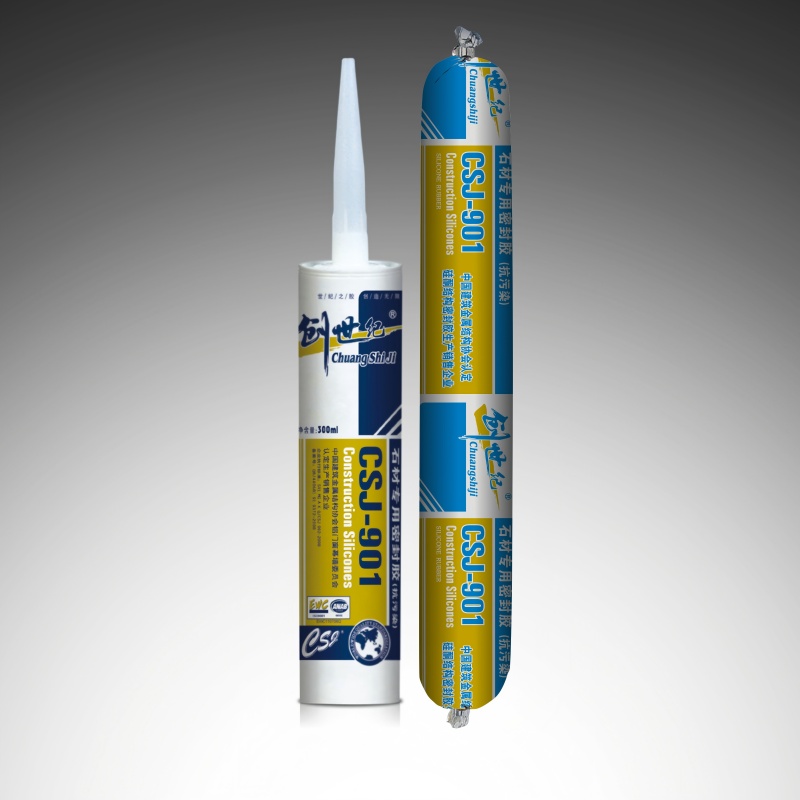
1. Turning “air” into “force”: the curing magic of one-component silicone glue
- The unique curing mechanism of one-component silicone glue is the basis for its wide application.
- Its core secret lies in contact with moisture in the air (moisture curing). The active groups in the liquid colloid undergo hydrolysis and condensation reactions with moisture to form a three-dimensional network structure, transforming from a paste to a tough elastic rubber body. This process does not require additional catalysts or complex equipment (two-component glue needs to be mixed), which greatly simplifies the construction process and makes it the first choice for DIY and on-site construction. Its curing depth and speed are significantly affected by the ambient temperature and humidity and the thickness of the glue seam.
2. Acidic glue vs. neutral glue: Corrosiveness defines the application boundary
- Acidity and alkalinity are the core yardsticks for distinguishing the scope of application of glass glue.
- Acidic glue: It releases acetic acid during curing and has a noticeable odor. Although it has strong adhesion to glass, ceramics, etc. and is relatively low in price, its strong corrosiveness is a fatal weakness. It corrodes metals (causing rust) and reacts with alkaline building materials such as cement (affecting bonding). It is mainly suitable for glass-to-glass, glass-to-ceramic bonding and sealing, or fixing of non-metallic parts (such as fabrics and plastic interiors) inside cars. Typical limitations: It must not be used for bonding metal door and window frames to glass, marble and other calcium carbonate-containing building materials, or inside electronic equipment.
- Neutral glue: No corrosive substances are released during the curing process, and the odor is mild. Its universal adaptability comes from overcoming the defects of acid glue: it does not corrode metals and has good compatibility with most building materials. It has a wide range of applications, covering metal door and window frames, non-structural parts of glass curtain walls, aluminum-plastic panels, stone, wood, PVC, clean environments, etc. Although the price is slightly higher, its safety and versatility make it the mainstream in the market. Authoritative reference: ASTM C920 standard specifies the performance requirements of elastic sealants for construction in detail, and neutral silicone glue is an important category that meets the standards.
3. Silicone structural sealant: the “steel bones” of curtain wall safety
- Silicone structural sealant is a high-performance member of the glass glue family, which is directly related to building safety.
- It is different from ordinary sealants. Its core mission is to bear the weight, wind load, earthquake effect, etc. of curtain wall glass panels for a long time and transfer them to the building support structure (structural bonding). This requires it to have:
- Ultra-high strength: Excellent tensile strength (much higher than ordinary glue) and bonding strength.
- Extreme durability: Super strong weather resistance (resistance to ultraviolet rays, extreme temperatures, rain erosion), fatigue resistance, and aging resistance.
- Strict certification: Must meet strict national/international standards (such as China GB 16776, US ASTM C1184). Its formulation, production, testing, and construction (professional qualifications are required) have the highest requirements, and the price is also much higher than ordinary glass glue. It is the key material that makes modern glass curtain walls light, transparent, safe and reliable.
4. Excellent performance: comprehensive protection beyond bonding
- The comprehensive performance of silicone glass glue makes it an “all-round guard” for buildings.
- Its advantages far exceed basic bonding:
- Elastic leakproof: After curing, it forms an elastomer that can effectively follow the displacement of the joint (thermal expansion and contraction, wind pressure deformation), provide long-lasting sealing, wind and rainproof, and leakproof (such as kitchens, roofs, windows).
- Environmental guardian: Excellent weather resistance (UV resistance, high and low temperature resistance – often up to -40℃ to 150℃), ozone resistance, moisture resistance, and mildew resistance (especially mildew-proof formulas) to ensure long-term performance stability. The U.S. Department of Energy pointed out that good sealing can significantly improve building energy efficiency.
- Construction-friendly: Good thixotropy, no sagging or flow when applying glue to the top seam or vertical seam, ensuring construction accuracy and beauty.
- Stable and reliable: High-quality products are still easy to extrude at low temperatures (such as below 0℃), and can also maintain stable performance at high temperatures (such as continuous 204℃).
5. Proper construction: Success or failure lies in details
- The performance of glass glue depends greatly on the correct construction process.
- Key steps determine the final effect:
- Substrate cleaning: It is the lifeline! Oil, dust, water stains, and old glue residues must be thoroughly removed. Use special cleaning agents (such as isopropyl alcohol) to ensure that the substrate is completely dry and solid.
- Gap preparation: The depth and width ratio is usually recommended to be 1:1 or 2:1. Too shallow or insufficient filling is prone to failure. If necessary, use backing material (closed-cell foam rod) to control the thickness of the glue seam (usually 5-15mm), ensure three-sided bonding (only two-sided bonding) and provide support.
- Standardized glue application: Use a glue gun to apply glue continuously at a uniform speed to ensure that the glue strip is full, continuous, and free of bubbles. The cross-section is preferably semicircular.
- Fine finishing: Before the surface dries (usually within 10-30 minutes), use special tools (scraper, tongue depressor dipped in soapy water) to compact, flatten and smooth the glue joints to enhance sealing, aesthetics and stain resistance.
- Full curing: The curing time is affected by temperature and humidity. Usually, it can be initially cured (touch dry) in 24 hours, reach practical strength in about 7 days, and fully cured in 21-28 days. Avoid external disturbance, contact with water or chemicals during curing.
6. Color aesthetics: visual expression beyond function
- The color selection of glass glue is an important link in achieving the unity of function and beauty.
- Conventional color system: Six colors, including black, porcelain white, transparent, silver gray, gray, and bronze, are the most commonly used to meet the needs of basic concealment (transparent, porcelain white) or emphasis on lines (black, gray).
- Customized colors: In pursuit of the ultimate design effect (such as special metal texture, perfect match with building materials or furniture colors), professional manufacturers can provide customized color matching services, turning practical sealing materials into design elements. The popular color trends of international color organizations such as Pantone may also affect the color selection of high-end customized glue.
- Visual considerations: Transparent glue is suitable for joints that want to be “invisible”; white/light-colored glue is often used for light-colored materials (such as white window frames, tiles); dark-colored glue is used for dark-colored materials or scenes that need to outline lines. Anti-mold glue is often available in white or transparent.
Summary: Glass glue, this seemingly inconspicuous building material auxiliary material, is actually the key “chemical rivet” and “elastic defense line” to build a safe, comfortable and durable building environment. Only by deeply understanding its core classification (single and double components), key properties (acidic/neutral/structural adhesives), excellent performance (bonding, sealing, weather resistance) and scientific application (selecting the right adhesive, making good substrates, and standardizing construction) can its value be maximized. From sealing the gap of a window in your home to supporting the glass curtain wall of a skyscraper, glass adhesive continues to inject invisible power and tangible beauty into modern architecture with its scientific formula, stable performance and evolving color aesthetics. Choosing glass adhesives with reliable quality and suitable matching, and strictly following construction specifications, is the fundamental way to ensure the long-term effectiveness of this “invisible protection”.